Additive manufacturing technology plays an important role in the sports industry. It can be used to design and customize all kinds of equipment. Among the many sports applications, 3D printed bikes are undoubtedly the most widespread. Using 3D printing technology can make a bike lighter, faster and more comfortable, while reducing manufacturing time and costs. The most commonly used materials are high performance -metals or composites. In addition, by 3D Scan, you can customize bicycle helmet, seat, handlebars and other accessories.
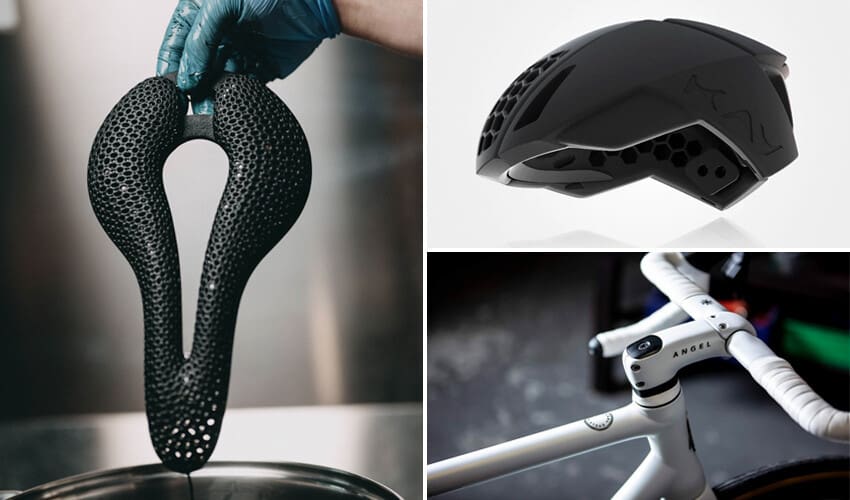
Angel Cycle Works: Angel Heaven Bike
Angel Heaven is a 3D-printed titanium alloy bike made by Spanish company Angel Cycle Works. In collaboration with the MADIT Metal 3D team, SLM 3D printing technology was used to create this unique bike. They use unique titanium powder, delicate structural design and manufacturing. The high precision of the 3D printer used, while the high hardness of the powder and its triple track support enable the reduction and elimination of unnecessary materials, creating a cutting-edge and durable product. Colleague, this manufacturing method can also reduce material waste, improve production efficiency and reduce costs. In general, Angel Heaven is a very distinctive bicycle brand. They use 3D printing technology to produce high-quality bicycle parts, so as to provide users with more personalized and high-quality riding experience.
△Angel Heaven, Titanium Alloy Bike (picture source: Angel Cycle Works)
Pinarello: Bolide F HR 3D
Bolide F HR 3D is Pinarello 3D printed bike
- The Bolide F HR 3D bike uses a double rear triangle design to improve stability and rigidity.
- Manufactured from Toray 1100 1k carbon fiber material, it has the characteristics of lightweight, high rigidity and high strength.
- Internal cabling and integrated brakes are used to reduce air resistance and provide riding efficiency.
- With a custom design and customised accessories, it can be adjusted and optimized according to the rider's needs to achieve the best performance and comfort.
- To make the bike, the bike's frame and front fork were 3D-printed using a laser powder bed fusion technology and an alloy called Scalmalloy, which is made up of scandium, aluminum and magnesium.
- The frame consists of just five individually produced pieces that are then glued together
Overall, the Bolide F HR 3D bike is a high-end competition bike that uses 3D printing technology, high quality materials and advanced design. With excellent performance and beautiful appearance, it is a standout product for Pinarello in the field of bicycle manufacturing.
△Pinarello 的 Bolide F HR 3D(picture source :Pinarello)
ELASTIC INTERFACE 3D printed liner
Italian company ELASTIC INTERFACE has developed the first 3D-printed suede cushion to provide better comfort and air permeability for cyclists. The NX3 suede pad incorporates a 3D-printed piece that replaces foam or padding commonly used in support areas. The lattice structure helps to control the density and hardness of the mat more precisely according to its purpose. In addition, the design allows the seat to deform freely under weight and pressure, which in turn results in greater cushioning, more stable performance, and less pad deformation. To make the suede pads, the company used FDM 3D printing technology.In this way, they managed to develop a grid shape. Due to hydrophobic properties, this promotes air permeability and prevents moisture accumulation. The product and all the research surrounding it aims not only to guarantee riders' performance, but also to find a solution to produce them with zero production waste. By going beyond what is available in the market, a new way of production can be devised.
△picture source: Elastic Interface
Shadow M1 -- 3D printed e-bikes for cities
The Shadow M1 is a 3D-printed e-bike from Belgian startup Shadow Concept. The company was set up with the goal of making 3D-printed, environmentally friendly, customized bikes. Built specifically for urban environments as an electric bike, the M1 features a 36 v 11.4ah(400 wh) battery that allows users to travel an average of 70 km, but can be upgraded to 100 km. In addition, it includes a 3D-printed frame that ADAPTS to each customer's physical characteristics, allowing the bike to be fully customized to your size, making it even more comfortable. To create the frame, Shadow used large-format FFF 3d printing and a CO2-neutral and biodegradable biopolymer. It also has hydraulic brakes and a rider - friendly seat. All in all, the bike strikes a good balance between comfort and environmental aspects, starting at €2,499 (HK $21,272.44).
△picture source: Shadow M1
Posedla: 3D printed bike seat cushion
Based in the Czech Republic, Posedla mission is to design the most suitable bike seat for all cyclists, regardless of their skill level. One way to do this is through additive manufacturing, where the saddle, called Joyseat, is made up of several elements, including a carbon shell and, in particular, a 3D-printed pad placed on top of the shell. The unit is printed with TPU-to ensure comfort and flexibility. Depending on the rider's parameters, the saddle weighs between 170 and 210 grams and has a length of 262 mm. Posedla offers an online configurator on its website, so everyone can design their own cushion according to their needs, capabilities and desires. Receiving such a piece at home costs €490 (HK $4,171.07).
Personomic: Customize the bike handle
Personomic, a young German startup, has developed a 3D-printed custom handle for hand pain avoidance and prevention. They are manufactured using Rapid Shape's DLP printers, producing grips that match the cyclist's hand. This allows for better distribution of pressure, avoids pressure spikes, and avoids pinching of nerves in the hand. This prevents hand pain and numbness after hours of cycling. In addition, the grip can be customized using the company's customization tool, and users can design the color and texture of the handle themselves. Finally, the silica-coated handles were also softer and did not become sticky due to weather or sun exposure, according to Personomic.
Specialized: 3D printed bike seat cushions
Specialized is a manufacturer of bike parts that works with Carbon to make the 3D-printed saddle. Called S-Works Power Saddle with Mirror Technology, the seat is designed to improve rider comfort, protection and performance. Its complex elastic carbon-based mesh structure provides better performance than traditional saddle materials such as foam. With 3d printing, Specialized is able to create multiple areas of varying densities and compliance, which allows riders to get support exactly where they need it.
△picture source: Specialized
Openbike project - Anyone can make a bike
Openbike is an open-source bike project started by Dutch designer Basten Leijh, which aims to use 3d printing technology to drive innovation and sustainability in the bike industry. The project offers a free and open design where anyone can build and assemble their own bike via a 3d printer. The Openbike project uses an open design based on CAD software to provide users with 3d printed design documents for a variety of bike parts. Users can download the design documents, use 3d printing technology to build the parts, and then follow the instructions to assemble a bike. The Openbike project's bikes are designed to be flexible, allowing users to modify and customize them according to their needs and preferences. For example, you can change the size and shape of the frame, choose different wheels, brakes, transmission and other components to achieve different riding requirements. In addition to design flexibility, the Openbike project has the advantage of sustainability. Because the bikes are made using 3d printing technology, the waste of discarded materials can be greatly reduced. In addition, the project encourages users to use waste materials as manufacturing materials for bicycle parts to minimize waste of resources. Overall, Openbike is an open source, flexible and sustainable bike project that uses 3d printing technology to provide users with more freedom and creativity. The project has brought new ideas and innovations to the cycling industry and is expected to drive sustainable development of bike manufacturing and cycling in the future.
Smart bicycle helmet PYLO
As PYLO grows, German company nFrontier wants to make cycling safer in order to truly become a more sustainable form of transport. This is done using AutoDesk 3dsmax software and manufacturer Stratasys' F370 and J55 3d printers. The helmet features an integrated self-deploying airbag that protects the driver's jaw, teeth and eyes in the event of an accident. In addition, the LED lights that come with the head and tail as well as the LED eye mask can be opened by double clicking. What makes PYLO stand out the most is its LIDAR (Light Detection and Ranging) technology, a safety system that warns riders when vehicles are approaching at very high speeds. In addition, it will inform riders of potential blind spot hazards and provide optimal conditions for accident prevention. The 3D-printed lining and the lightweight material used to make the helmet won't hold the head down, making the bike a comfortable and safe means of transportation -- for athletes and recreational cyclists alike.
△picture source: Pylo
3D printed spare parts for Mythos
Mythos showed off its first 3D printed bike spare in 2021, which connects the handlebars to the pivot of the bike's front fork. The component, called Elix, is printed on a metal 3D printer with a 15% increase in torsional stiffness. In 2022, Mythos launched a new 3D printed spare part, IXO, printed on an EBM (electron beam melting) machine using an aerospace certified titanium alloy that weighs just 147g and increases torsional stiffness by 16% and bending stiffness by 11%.
△La potence IXO imprimée en 3D(picture source: Mythos)
KAV: 3D printed bike helmet
KAV Sports has built on its work in creating 3D-printed hockey helmets to develop a 3D-printed helmet that is not only customizable compared to many others, but also streamlined and lightweight, and safer. To achieve this, KAV used 3d printing to create honeycomb structures within the helmet, adding additional reinforcement in key areas, making the helmet significantly more than 25 to 50 percent above helmet certification standards.
A Montain bike with an all-carbon fiber suspension
Revel aims to demonstrate the potential of additive manufacturing in building carbon fiber bikes. Jordan Haffener, chief engineer at Revel Bikes, designed and worked on the Rodeo concept. To that end, they partnered with Arevo Inc., a 3D printing specialist, to make carbon-fiber reinforced bicycle frames. Moreover, this is not just a show bike, but a fully functional concept car. Through this innovative project, Revel aims to push the boundaries of innovation in additive manufacturing in mountain biking.
△picture source: Revel Bikes
INDEXLAB, XGINEERING and GIMAC collaborate on the "New01Bike" project
The new project, called New01bike, aims to build fully functional bikes using only recycled materials, promoting sustainability and circular economy practices in manufacturing. According to its creators, it is the first ever 3D printed bicycle frame made from recycled polycarbonate material and is a milestone in the development of cycling. The framework was designed in a research lab by Italian startup INDEXLAB and manufactured using a polymer extrusion process. Using shredded and melted waste polycarbonate items such as CD, safety glasses and water bottles, materials for the conformable RAM (robotic additive molding) process were created. The technology, led by XGINEERING and GIMAC in collaboration with INDEXLAB, is gaining popularity in the automotive sector due to its speed, waste reduction and ability to customize unique parts.
△picture source: INDEXLAB
Canyon 3D printed bike prototype
Canyon unveiled its first 3D printed bike prototype in 2022. This is made in three parts by a 3d printing service provider, each of which takes six hours to complete. Canyon goal with the bike is to create a more sustainable bike. This is because the powder bed fusion solution used reduces the amount of material required, bringing the weight of the device down to under 2kg. At the same time, due to the lattice structure of the frame, which can guarantee high performance, recycled aluminum was chosen as the material.
△picture source: Canyon
VAEN: 3D printed bike seat cushion
Designer Vasi Ganhi used 3d printing to create VAEN Bike seat cushion, which mimics organic shapes by using gridded foam in the middle layer of the bike seat. The whole seat is cushioned, while the outer layer is comfortable, breathable and has some resistance. The use of additive manufacturing makes it possible to customise the saddle for the rider, thereby maximising performance for the user. The bike's pads come in black, yellow, glass, blue and orange, and users can choose according to their preferences.
△picture source: VAEN
Source: 南極熊